Investment Casting 101: The Lost Wax Manufacturing Process Explained
- Locke-Brothers
- Feb 28, 2022
- 3 min read
Updated: Mar 3, 2022

Investment casting is a manufacturing process used for casting complex shapes that can help eliminate costly machining, improve surface finishes, while achieving tight tolerances. It can provide a near net shape part in both ferrous and non-ferrous alloys.
Here is a quick review of this casting process:
Heated wax is injected into the tools cavity(s) which contains the geometry of the part to be produced.
After the injected wax has cooled, it is removed from the tool and assembled onto ‘trees.’ A liquid adhesive is applied to the tree which secures, the next step, a sand coating.
Several sand coatings are applied to the wax patterns which creates a shell around the wax.
The wax is melted, and the remaining sand shell is the ‘pattern,’ use to produce your raw casting.
Each casting process is explained in more detail in this article.
History of the Investment Casting
The Investment Casting Process (Lost Wax) is over 5,000 years old. The Ancient Egyptians used beeswax patterns to create jewelry and other ornaments. The Ancient Greeks and Romans used what was called 'hollow casting' to create bronze statues.

Today, these types or parts can be made from an investment casting process:
Motor Box Housings
Covers
Pumps
Sensors
Medical Devices
Agricultural Components
Electrical Assemblies

The Investment Casting Process:
Part Design
The process starts with a review of the customer’s proposed part design. Our engineering team will work with your design team to help improve the design to eliminate unnecessary costs as well as increase the overall part quality.
Tooling
The tooling design and construction is key to providing a quality casting! Gate size and location(s), the area in which the wax is ‘invested’ in the tool, is critical in providing a quality wax pattern. Tools can consist of a single wax cavity or multiple cavities. This is primarily dependent on the part size and the EAU.
Tree Assembly
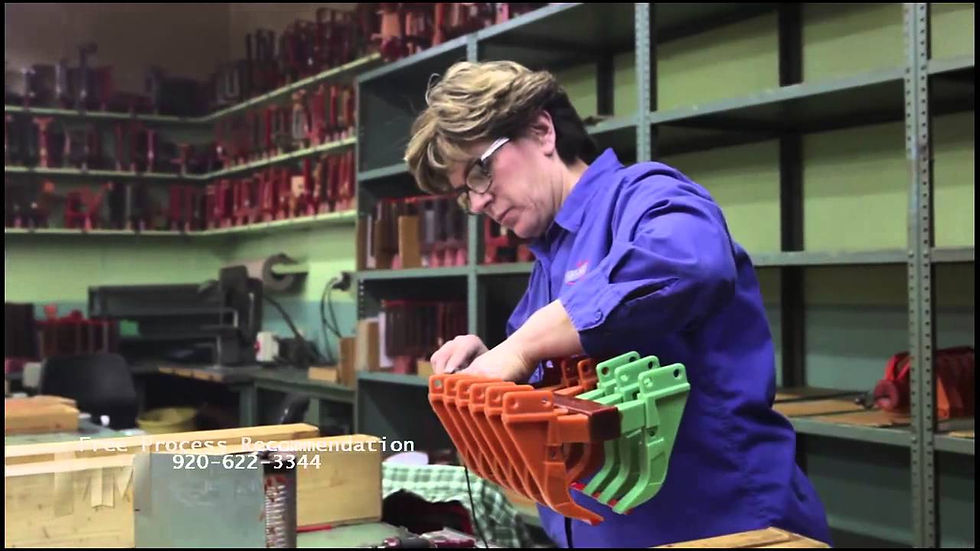
After the wax patterns have been completed, they are attached to a “tree’. A tree provides the support system for the molten metal to flow into the wax patterns. The amount of wax patterns, assembled to the trees, will depend on the size or weight of the casting.
Investing
The tree (with attached patterns) is dipped into a liquid slurry that provides an adhesive layer to the wax patterns. The tree is then coated with layers of silica material (sand). This process is repeated, with progressively coarser grades of silica.
De-Waxing
After the tree is thoroughly coated, it is placed in an autoclave (Oven) and the coated wax is melted out leaving a ‘sand mold’.
Firing

The trees are now placed in a firing furnace. This heating process improves the flow of the molten material that will be poured into them. It also changes the silicon material into a ceramic coating.
Casting

The molds are removed, one by one, from the firing furnace and the molten metal is immediately poured and set aside to cool.
Finishing
The castings are cut away from the tree and variety of cleaning operations take place to remove cores and the ceramic coating.
Inspection
Every casting is visually inspected, and all critical dimensions are checked with the proper inspection equipment. We use a continuous quality monitoring system to insure ever casting is made to the highest quality.
10 Key Benefits of Investment Castings vs Other Casting Processes
Lower cost tooling
Able to cast-in complex internal feature
Near net shape dimensions
Hold close tolerances (+/_.005” [.127mm] per inch, standard)
Superior As-Cast surface finish
Rich choice of alloys (100+ allow choices)
Strong material choices
Achieve fine details
Minimize needed secondary operations
Cast thinner walls
Bonus Benefits
When rapid prototype or only a few parts are needed. The wax patterns can be 3D printed eliminating the need for tooling. This is a great option when the design is not fully vetted or if parts are needed ASAP.
Locke-Brothers Choice for Investment Casting
Locke-Brothers has been partnered with Shelmet Precision Casting for 52 years; our partnership started in 1970 when our agency was first established. Shelmet Precision Casting Company has specialized in investment castings since 1960.
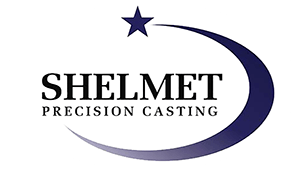
Supplier Overview:
Shelmet is a leading American investment casting manufacturer. Often referred to as the lost wax method, Shelmet has internally refined the investment casting process and specializes in short-to-medium-run orders. Shelmet is a non-union, family-owned shop that has a strong emphasis on customer satisfaction.
留言