Are You Using the Best Manufacturing Process Possible for Your Part Design?
- Locke-Brothers
- Aug 3, 2022
- 1 min read
With the current labor shortage and material pricing at an all-time high, it might be wise to assess the current manufacturing process of high cost, higher volume parts to verify that they are being made in the correct manufacturing process.

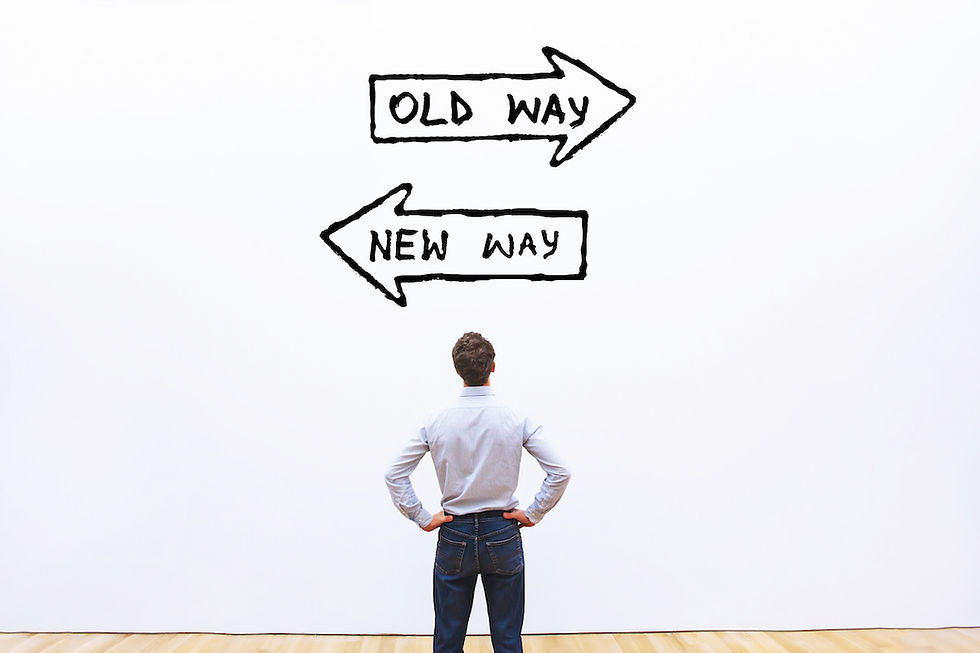
Locke-Brothers has been very successful at helping our customers convert parts from one manufacturing process to another to help lower cost, improve lead time, and/or improve overall part quality.
With today’s labor shortage, this has become more important today than ever. Shortening the supply chain lead time or reduce SKUs can drastically reduce the number of workers needed to produce/assemble your product.

Cost Saving Case Study
Our team has helped one of our customers, in the Industrial Tool market, convert an assembly into an investment casting.

The original design assembly used 12 different components manufactured from five separate processes.
With a little design help, Shelmet was able to cast this as a one-piece steel casting, eliminating 11 SKUs and drastically reducing the needed assembly time.
With this new design, the OEM (Original Equipment Manufacturer) has realized a cost savings while being able to improve the overall quality and aesthetics of the product while providing a competitively priced component to the market and under their original budget.
Finest Quality Parts. Competitive Pricing On Time Delivery.
Locke-Brothers and our manufacturing partners are always here to help improve your part design. Please let us know if you would like us to review any current or new project for cost saving opportunities or quality improvements.
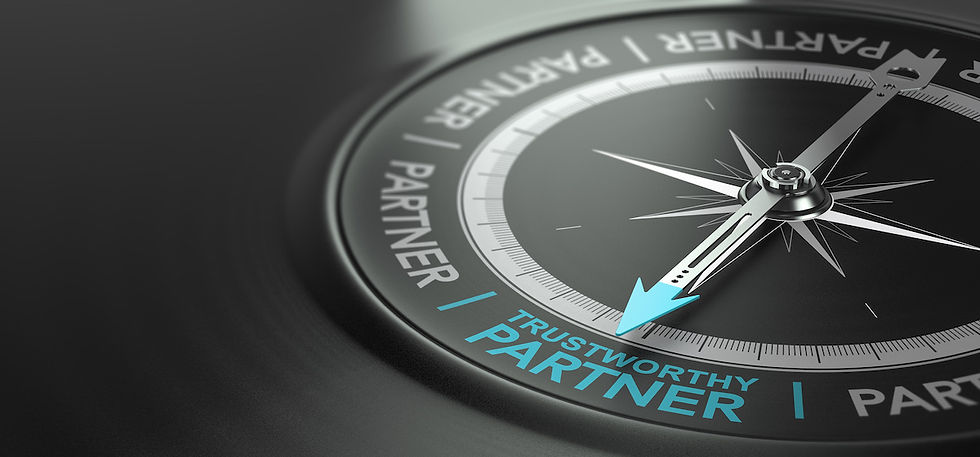
Comments